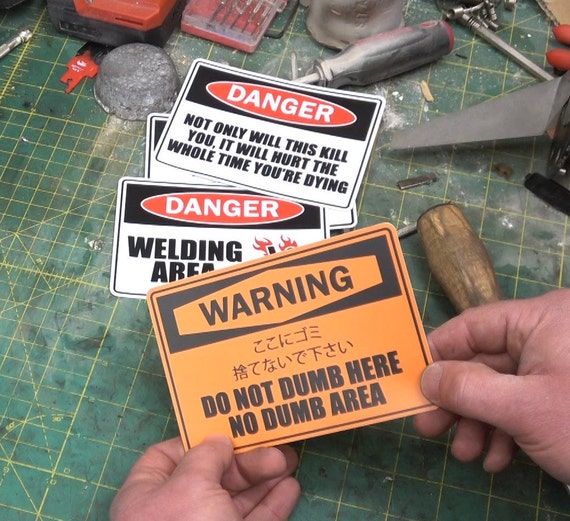
I’ve never been accused of being a genius, but there I was today putting some safety wire on an oil sump fitting that had been forgotten. Don’t worry the plane hasn’t flown yet.
Anyways, there’s these six little bolts that go through a flange and thread into the cast sump. On my last hangar adventure I found four of them had never been installed and you guessed it, they don’t go into blind holes but holes that run all the way clear to the engine oil above. Guess how I found that out. Oil-dry is neat stuff and what’s thirty bucks of Aeroshell on the floor between friends? Extra bolts located and installed, oil level serviced to the full 8 litres, but then it was time to leave. So today I’m trying to remember how to wrap safety wire and contorting to do something that should have been done with the engine on a stand and generally cursing the guy who forgot.
Five of the six bolts had drilled heads while the sixth did not. No biggie, I’ll just pull the bolt, head down to the hardware room, grab another with a drilled head, then install and wire. Oil dry is neat stuff.
I didn’t lose much that time around. It was pretty obvious what I had done so it was like a tablespoon or two. Still, what a dumbass move.